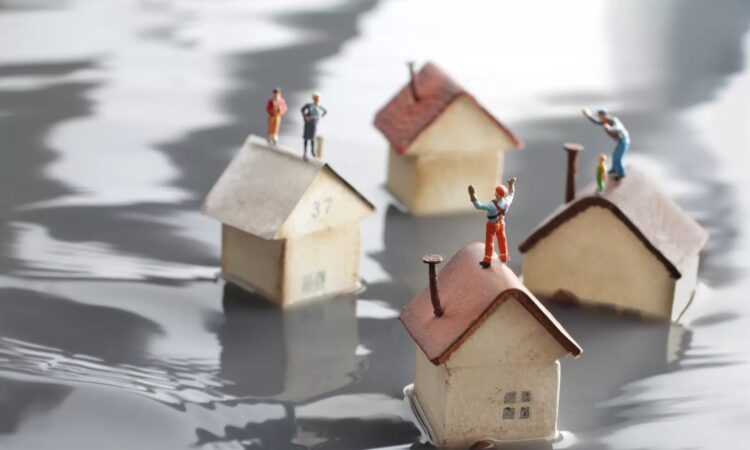
When flood waters or water leaks damage a home or business in Orlando, proper drying is crucial to restore the structure and prevent mold growth. Water mitigation companies use powerful truck-mounted equipment and advanced drying techniques to thoroughly dry out flooded properties. The methods used make the difference between effective restoration and destructive mold taking hold.
Extraction
The first step is always extracting as much water as possible using professional suctioning equipment. Truck-mounted vacuum systems rapidly remove standing water. For carpeted areas, extraction tools pull water from the carpet pad and flooring below. The goal is to remove excess moisture to facilitate faster drying.
Structural drying
Before drying interior finishing, it’s critical to dry any wet structural components like wood framing. Companies use air movers and dehumidifiers to circulate air and slowly lower humidity at the structure’s core. Where moisture readings are high, they may cut small drying holes to insert drying equipment. Thorough structural drying prevents future mold and instability.
Surface drying and scrubbing
After water extraction, surfaces are thoroughly dried using specialized equipment. Air movers direct high-velocity air across floors, walls, and other materials to accelerate evaporation. Companies also use industrial air scrubbers that circulate and filter air to remove moisture. For textiles and upholstery, they use vacuum extractors to deep clean and dry in one process look at here now www.damagecontrol-911.com/.
Dehumidification
Industrial dehumidifiers are continually run throughout drying to remove moisture from the air. Lower humidity accelerates evaporation from soaked materials. Contractors use humidity sensors and hygrometers to monitor moisture content in the air until it reaches normal indoor levels of around 30-50%. Proper dehumidification prevents remaining moisture from being reabsorbed into dried materials.
Desiccant Drying
Drying in tight spaces like walls or under floors, desiccant drying may be used. It involves placing natural or synthetic beads that attract and absorb moisture in the space. Air movers circulate air to continuously pull moisture into the desiccant. This method dries hidden moist areas that other techniques cannot reach.
Insulation drying
Wet insulation in walls and attics easily harbors mold, so companies use insulation drying equipment. Plastic tubing inserted into the insulation blows heated, dehumidified air to dry it without removal. For moldy insulation, removal, and replacement are recommended. Air scrubbers filter airborne mold spores during removal to prevent spreading.
Monitoring and testing
Throughout the drying process, companies use moisture meters, infrared cameras, hygrometers, and humidity sensors to find moisture and monitor drying progress. Once all areas are measured dry for 48-72 hours, final moisture mapping is done to verify. Only once their strict dryness standards are met do they approve reconstruction to begin.
Mold treatment
If initial drying does not start quickly, surfaces with mold growth may need specialized mold treatment. Any porous materials with heavy mold are discarded. The remaining surfaces are scrubbed and then treated with an EPA-registered antimicrobial to kill mold. HEPA vacuuming ensures spores are not released into the air. Air scrubbers also filter mold spores long-term.
Odor control
Flood damage often creates unpleasant odors that linger even once underlying moisture is removed. Water mitigation companies run industrial ozone generators that oxidize odor molecules and refresh indoor air quality. For extreme odors, they may use a fogging method to permeate the air with deodorizers.
Monitoring and control
After the initial drying process, companies continue to monitor both humidity levels and moisture content in materials using moisture meters. They keep equipment running until conditions stabilize. Most provide remote monitoring so any changes trigger a proactive response.